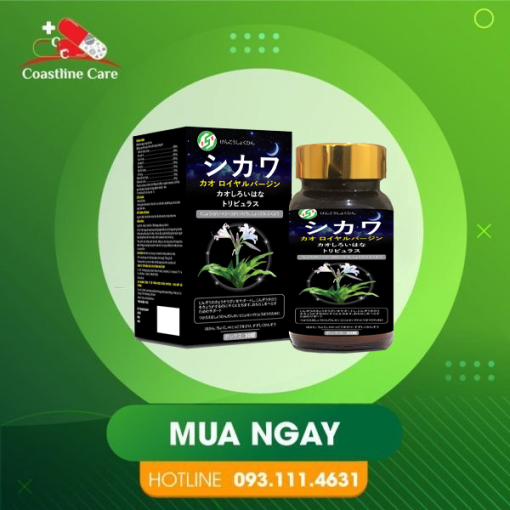
Branching out from the key dilemma, you are able to make a process map to check different prospective causes. Using a system map, you may identify the gaps with your procedure that may cause your trouble’s root result in.
Method – This branch contains every one of the methods and techniques involved in the method or exercise, in addition to the devices, components, and workflow.
Below, Each and every hypothesis in the Ishikawa diagram is prioritized and the highest precedence hypotheses are assigned steps, someone to carry them out, and also a owing date. This causes it to be less complicated for your staff chief to trace steps and see the effects of finished steps.
In this example, lighting could bring about an staff to produce a miscalculation causing an element not thoroughly installed. Therefore, the element not properly installed could be detailed inside the Ishikawa diagram.
Simply just investigating the lighting could just take time and means away from the investigation so step one could well be to determine if a component is mounted.
Then again, there are definitely places in my Ishikawa travel tutorial which can be significantly exterior the middle of Kanazawa. And every single one of these is worth going to.
Be certain that Every person on the group understands the condition in the identical way. Use a dilemma statement in order that everyone is on a similar webpage.
This diagram is among 7 top quality resources, a list of necessary methodologies for nha thuoc tay constant method enhancement. Right now, the Ishikawa Diagram remains a essential Device for figuring out root leads to and enabling systematic trouble-fixing, specifically in production and functions procedures.
Aspects during the Ishikawa diagram should be capable nha thuoc tay of make clear how the failure took place. By way of example, “lighting” is an average illustration below “setting”; having said that, it's seldom very clear how lights may lead to failure. As a substitute, the result of negative lighting needs to be detailed after which empirically investigated.
A production plant was experiencing quality Regulate difficulties with their solutions. The trouble was recognized making use of an Ishikawa Diagram, which assisted the workforce to recognize the likely leads to of the issue.
In venture administration, where by precision and systematic issue resolving are paramount, the fishbone diagram finds major utility. Venture delays, Charge overruns and unmet targets normally have multifaceted root causes.
Underneath is really an example of a fishbone diagram for the production enterprise. Within nha thuoc tay this circumstance, the company makes use of the 6Ms to raised comprehend the brings about of the condition, and that is that a part of the item is in the wrong dimensions.
The disciplined and structured surroundings from the military motivated his methodical method of dilemma-resolving.
Prenons l’exemple d’un cafe qui constate une baisse de fréquentation de son établissement. Pour identifier les results in de cet effet, ce restaurant peut utiliser le diagramme d’Ishikawa.